- 22 de junho de 2020
- Posted by: wcbm
- Category: Metodologia Lean
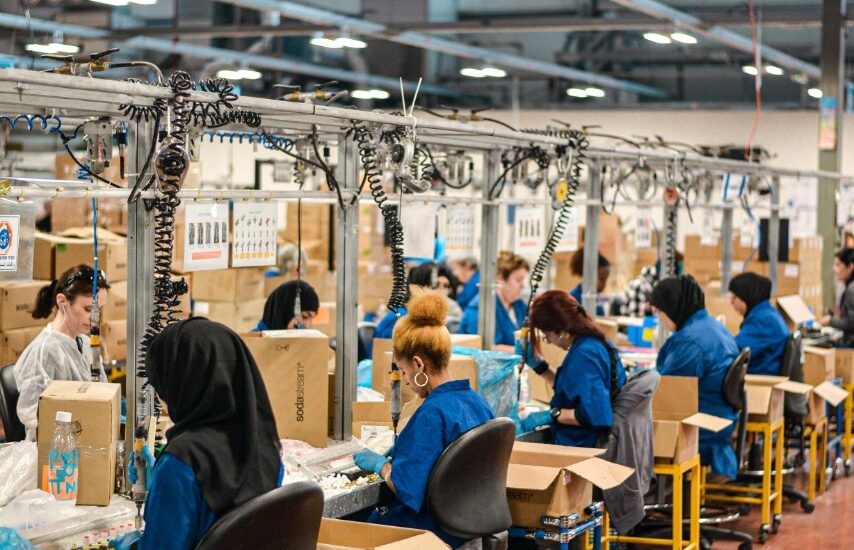
O que se entende por Produtividade?
Pela abrangência do tema há várias definições entre as quais as mais conhecidas são:
- “fazer o mesmo com menos”, e melhor,
- “fazer mais com menos”
Tudo isso sem matar ninguém de tanto trabalhar ou colocar em risco de acidente e saúde ocupacional, preservando os ativos da empresa e o meio ambiente.
O que é o balanceamento da mão de obra direta?
Trata-se de uma técnica utilizada para calcular a quantidade de operadores por turno de trabalho para atender a necessidade do cliente.
PASSO 1 – Calcular o Tempo Takt (TT):
Tempo Takt é o “ritmo” de trabalho para atender a necessidade do cliente.
A unidade do tempo Takt é em “tempo/peça”.
* o período de tempo tem que ser o mesmo no numerador e no denominador, mas a base além de dia, pode ser semana, quinzena ou mês.
Considerando-se uma célula de embalagem com 2 operadores:
- Número de turnos de trabalho por dia: 2
- Total de horas por turno: 8 horas/turno
- Refeição: 1 hora por turno
- Limpeza: 30 minutos por turno
- Ginástica laboral: 45 min/turno (15 minutos a cada 2 horas)
- Tempo Operacional Líquido (convertido na base segundos/dia):
= (2x8x3.600) – (2x1x3.600) – (2×0,5×3.600) – (2×0,75×3.600) =
= 57.600 – 7.200 – 3.600 – 5.400 = 41.400 segundos/dia
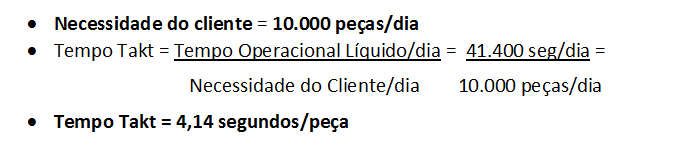
Ou seja, este é o ritmo de trabalho para atender a necessidade do cliente: 1 peça a cada 4,14 segundos (o equivalente a 870 peças/hora).
PASSO 2 – Medir os Tempos de Ciclo de cada Operador (TCO)
Trata-se do tempo de todas as atividades que o operador executa, exceto o tempo em que fica parado sem fazer nada (espera). O tempo medido deve sempre ser expresso na base de 1 peça.
Neste exemplo, os 2 operadores executam as mesmas atividades: embalar uma peça em uma caixa individual que é colocada em uma embalagem coletiva, que ao completar 10 unidades na embalagem coletiva, o operador deve fechar e identificar a embalagem coletiva e acomodá-la em um palete. Em seguida, caminha e pega outra embalagem coletiva, monta e posiciona no seu posto de trabalho, repetindo este ciclo durante todo o turno de trabalho.
Neste caso, o tempo de ciclo de cada operador é constituído de dois tempos:
- Embalagem individual: cada um dos 2 operadores leva 5 segundos para embalar uma peça na caixa individual;
- Embalagem coletiva: cada um dos 2 operadores ao preencher a embalagem coletiva com 10 caixas individuais, leva 1 minuto para fechar, identificar e levar a embalagem coletiva para um palete; caminhando e pegando outra embalagem coletiva, armando e posicionando para seguir embalando individualmente as peças e colocando na embalagem coletiva.
O primeiro impulso é somar os dois tempos (5 segundos + 1 minuto), o que está errado!
- 5 segundos são por peça embalada em caixa individual. Este tempo está correto (5 segundos/peça)
- mas o tempo de 1 minuto é por uma série de atividades de cada operador referente a uma embalagem que contém 10 peças embaladas em caixas individuais.
- Assim deve-se dividir 1 minuto (= 60 segundos) pelas 10 peças da embalagem coletiva a fim de converter em tempo equivalente a 1 peça (= 6 segundos/peça).
Agora podemos somar os dois tempos (5 + 6) segundos/peça, resultando no Tempo de Ciclo de cada um dos operadores. TCO = 11 segundos/peça
PASSO 3 – Plotar o gráfico “Tempo Takt vs Tempo de Ciclo do Operador”
Ao plotar o Gráfico Tempo Takt vs Tempo de Ciclo do Operador, para este caso em particular, onde os dois operadores executam exatamente as mesmas atividades, não devemos fazer como no gráfico da Fig. 1, e sim como o da Fig.2.
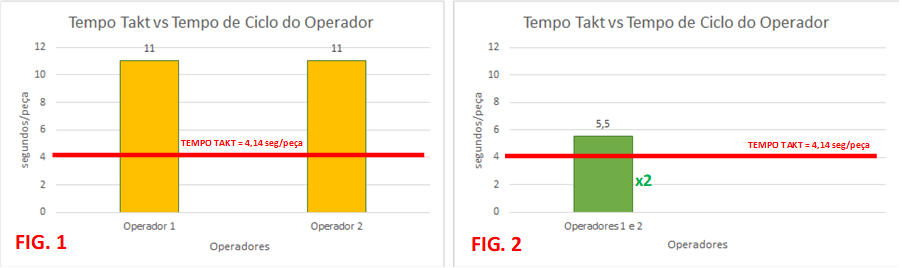
A Fig. 2 nos mostra que há um “gargalo” na mão de obra direta, uma vez que os 2 operadores embalam o equivalente a 1 peça em 5,5 segundos, quando deveriam embalar em 4,14 segundos/peça para atender a necessidade do cliente.
PASSO 4 – Calcular a Necessidade de Mão de Obra Direta por Turno
Utilize a seguinte fórmula:
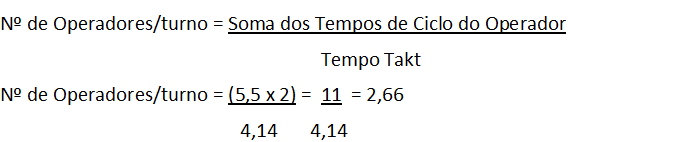
Nº de Operadores/turno = 2,66 operadores/turno
OBS: nº de operadores por turno atual = 2
PASSO 5 – Efetuar ajustes na mão de obra direta
Antes de contratar ou realocar mais um operador nesta célula, algumas ações de melhorias podem reduzir o tempo de ciclo dos operadores em 2,72 seg./peça, eliminando o “gargalo” de mão de obra direta, que também pode ser visualizado no gráfico da Fig. 2.
Exemplos de Possíveis Melhorias:
- Implementar melhorias no lay out quanto à apresentação de materiais, ferramentas e dispositivos, para que os operadores caminhem menos possível ao desempenhar suas atividades, e tenham uma melhor ergonomia e condições de segurança do trabalho
- adotar o critério do “operador-cirurgião”, ou seja, operador deve apenas operar, e alguém leva e traz tudo o que ele precisa. Afinal, operador caminhando não opera, não operando não produz, e não produzindo o cliente não recebe o seu produto.
Conclusão:
Que tal praticar o balanceamento da mão de obra direta em alguma célula ou linha? Comece por algo mais simples, e depois evolua para algo mais complexo.
Aprenda fazendo!
Mas não se esqueça de medir e analisar os resultados obtidos e efetuar correção de rumo para sustentar e melhorar continuamente a Produtividade na sua Empresa.
Fale Conosco:
Se você quiser conversar sobre este ou outro tema da sua necessidade, clique aqui https://www.wcbmconsulting.com/contato e deixe a sua mensagem.
Siga a gente nas redes sociais para ter acessos a mais conteúdos exclusivos!
Facebook: http://bit.ly/FacebookWCBM LinkedIn: http://bit.ly/LinkedInWCBM
Washington Kusabara
Sócio Diretor e Consultor
Thanks to Remy Gieling for sharing their work on Unsplash.